Dual-gradient drilling covers a variety of methods for managing pressure within an offshore well while drilling. Dual refers to systems built to reduce or eliminate the pressure added by drilling fluid in the riser. The goal is to create distinct pressure gradients above and below the mudline.
It is a departure from the simpler traditional approach using a single fluid combining water or oil plus drilling mud to make it viscous enough to remove cuttings while drilling, and just heavy enough to control pressures in the open hole without causing damage.
As drilling moved into deeper waters the gap has narrowed between the effective mud weight-per-gallon to offset the formation pressure, and the level that can fracture it. Drillers refer to this slim margin as working within tight drilling windows.
Drilling on a platform floating in deep water magnifies the difficulties of precisely managing the pressure in wells drilled through unpredictable, sometimes weak rock. The seemingly simple goal of, for example, creating a fluid with a mud weight of 13.5 lb/gal is complicated by long return trips to the drilling rigs that include risers that can be a mile or more long. There are two factors at work:
- The long riser adds to the pressure exerted on fluid in the well. Drillers adjust by using fluids with a lower mud weight to ensure the force it exerts is within the drilling window.
- The friction encountered as the fluid returns up the annulus adds to the pressure the formation “sees” while it is moving, which is known as the equivalent circulating density (ECD).
To demonstrate the effect of increasing water depth, Ken Smith, manager dual-gradient drilling implementation at Chevron, presented a slide showing how the drilling window would narrow if a field was moved into deeper water.
A study cited by Lance Labiche, chief of district operations support section for the US Bureau of Safety and Environmental Enforcement’s Gulf of Mexico Outer Continental Shelf Region, showed that about 400 wells drilled over the last 10 years in the Gulf of Mexico had a drilling window of 0.5 lb/gal, which the agency has set as its minimum safe margin.
“While it is safe to drill these wells with a 0.5 ppg drilling margin, they are nearing the limits of being drillable using conventional drilling practices,” Labiche said. “Dual-gradient drilling has the potential of helping manage the problem of tighter drilling margins as we move to deeper water and drill through more depleted sands.”
Managed-Pressure Drilling MethodsConstant Bottom Hole Pressure—for drilling in narrow and/or relatively unknown safe mud weight windows…-narrow drilling margins that manifest kick-loss scenarios. Pressurized Mud Cap—for drilling in rock where there have been problems with severe to total loss of drilling fluid circulation. Returns Flow Control—closed-loop systems with early kick-loss detection capabilities used to enhance drilling safety and limit environmental risks. Dual Gradient—used for offshore on wells to reduce the impact of the riser on the effective mud weight and -control pressures within narrow drilling margin. |
Casing Limits
Narrow drilling margins lead narrowing holes. Complex casing designs are a tangible indication of the many problems encountered drilling in formations where tight drilling windows are combined with other challenges, ranging from fractured carbonates to unexpected changes in pressures that can cause a kick, which is an influx into an open hole that must be controlled to ensure it does not grow into a blowout.
Adding sections of casing stabilizes the hole, but there is a downside. Each string of casing is narrower than the previous one so it can be moved into place. In deepwater wells the tight pressure margins require many strings to be set, with 10 or more in some cases.
Drillers have worked to minimize the problem by using techniques to strengthen the borehole or limit narrowing with expandable casing, but there is a limit to the relief those can offer. Managing pressure while drilling at depths where the pore pressure in the rock can change unexpectedly is like moving a piano through a tight passage on a bobbing ship. It is hard to avoid bumping into limits, and when that happens the damage can be lasting.
“The formation will see big pressure and small pressure. All those fluctuations stress formations,” said Uno Holm Rognli, vice president of drilling and wells offshore US at Statoil.
Full or Partial
Dual-gradient systems attack the problems peculiar to these wells in a variety of ways. The differences reflect the multiple factors determining the pressure exerted by the drilling fluid and design tradeoffs reflecting the cost and complexity of these approaches.
The version known as full dual gradient moves an enormous mud pump to the seafloor. Drilling fluid and cuttings are removed from the riser after the blowout preventer and lifted up in a 6-in. pipe to the drillship.
A barrier separating the well from the riser during dual-gradient drilling, allows the annular above the mudline, normally used for fluid returns, to be filled with a seawater-weight fluid. Removing the weight of the riser, and managing the pump speed, widens the drilling window, and allows heavier weight fluid.
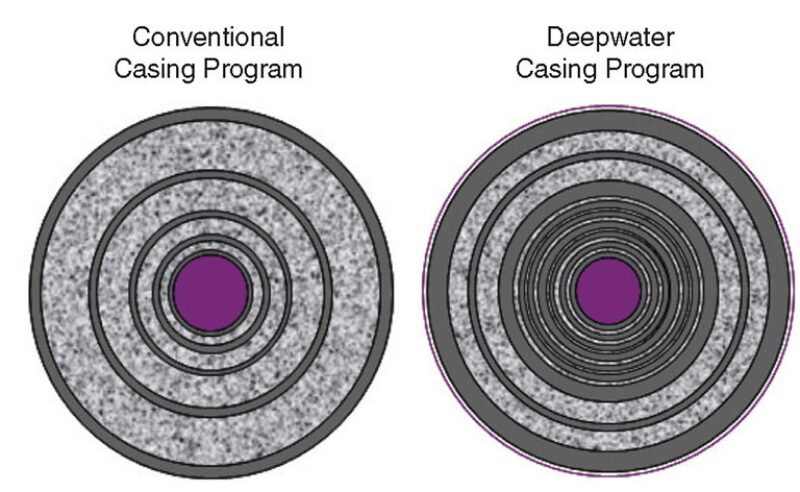
“The bottomhole pressure is the same—dual gradient or conventional—but denser mud is used which is much more in harmony with nature,” Smith said. “You remove the problem of water depth.”
The second dual gradient approach now in use also uses a pump to lighten the riser, but it is located on the riser about 1,000 ft below the surface. Normally there is air in the riser above the fluid level, which is adjusted up and down to manage the downhole pressure.
For Statoil, the biggest backer of what is known as a mid-riser system, the appeal of the pump is its ability to quickly adjust the pressure in the well by raising and lowering the fluid column using the pump. Speeding the pumping rate lowers the fluid level and the pressure in the well, slowing it allows the column of fluid to rise, increasing the effective pressure.
There is a direct correlation between pressure changes measured by sensors in the riser and in the bottomhole pressure, said Roger Stave, a senior technology adviser at Enhanced Drilling, which was formerly part of AGR Group.
It is called the EC-Drill system, which refers to how changing pump speeds can vary the effective pressure by changing the ECD. This adjustment can be made in minutes, a fraction of the time needed to reach the same goal by adding mud and waiting for it to circulate through a well, Rognli said.
The Chevron system also can alter the pressure by changing pump speeds, and can do so faster than the EC-Drill system. Both systems can be programmed to manage fluid flows using real-time information.
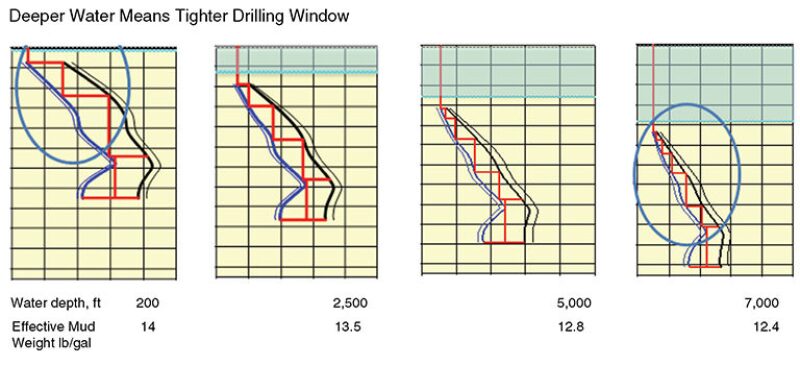
Orphan Technologies
The dual-gradient evolutionary tree includes branches that stopped growing years ago. Some appear dead, such as adding hollow glass balls to lighten fluids in the drilling riser, while others could be resuscitated with support from a backer, such as reducing the weight of the fluid in the riser by pumping in a lighter liquid into the riser.
Transocean developed that idea as a way around one of the big obstacles to dual gradient—the large amount of equipment and installation time required by some approaches. “One roadblock has been finding a practical dual-gradient method using available rigs without enormous modification,” said John Kozicz, technology manager at Transocean. The company’s goal was to create a relatively simple system that could be installed in 3 to 4 weeks.
The system pumped a lighter fluid into the fluid as it rose within the riser, and then directed it through a separator that removed it for reuse. The benefit was it could significantly reduce the impact of the riser on drilling margins, he said.
It was built and installed on a drillship, Discoverer Enterprise in 2009, but before it was ever used disaster struck. The vessel was pressed into service after the destruction of Transocean’s Deepwater Horizon in 2010. The dual-gradient equipment was removed to clear space and has remained in storage ever since.
That disaster ushered in major changes in offshore drilling regulation. Drillers have been focused on complying with those changes as they geared up to resume work in the Gulf of Mexico. The future for Transocean’s idea, and the other varieties, will depend on finding operators willing to champion ideas with long-term commitments. “It is now coming up because of demand by operators,” Kozicz said. “We need the Chevrons of the world to provide a push.”
For Further Reading
OTC 25292 ECD Management Toolbox for Floating Drilling Units by John-Morten Godhavn, Statoil; Roger Stave, Enhanced Drilling, et al.
OTC 25256 Enhancing Well Control Through Managed-Pressure Drilling by Oscar Gabaldon, Martin Culen, Pat Brand, Blade Energy Partners.
SPE 164561 Successful Application of Deepwater Dual-Gradient Drilling by Paul Richard Ashley, Petronas; Roger Stave, Enhanced Drilling; Robert Ziegler, Petronas, et al.
OTC 22889 A Step Change in Safety: Drilling Deepwater Wells with Riser Margin by Robert Ziegler, Petronas.
SPE 163523 Operational Reliability Assessment of Conventional Drilling vs. MPD on Challenging Offshore Wells by Don Hannegan, Weatherford.